The resulting cladding layer was nicely bonded, and the blades exhibited improved fatigue traits in contrast with blades fashioned by the conventional silver brazing course of. laser beam. The alloy was overlaid on the metal as a powder layer 2.5 mm thick. After melting and bonding by the laser, the alloy layer was 1.5 mm thick and had little or no dilution from the metal. The resulting floor had excellent put on resistance.
The full melting of the filler ends in a dense layer with optimum adhesion to the substrate. The commonest software is for the damage protection, e.g. of instruments, but in addition corrosion safety or high temperature resistance can be particularly improved. Common hard alloys primarily based on cobalt, nickel and iron are used with and without the addition of onerous materials. But also specifically adapted materials could be utilized.
The constants a and b are primary properties of the fabric and can be decided from standard laboratory experiments on contemporary gasoline. In explosive welding, a compression force created by detonation of explosives is used to affix overlapping metal sheets. The becoming a member of parts are organized towards each other at an angle of 1–15°, relying on the material and method, and are prepared with a layer of explosive on the highest. After ignition the becoming a member of areas are moved against one another at excessive velocity.
As a remedy, fast cooling of the Zry ingot throughout fabrication (referred to as beta quenching) produces a much finer intermetallic precipitate population. This distribution of the transition metals maintains the strength of the Zry but improves its corrosion resistance, possibly by brief-circuiting cost-transport paths between the size surface and the steel–oxide interface. In order to eliminate waterside corrosion of cladding as a life-limiting process, modified Zircaloys have been developed. Under PWR water conditions, lowering the tin content material of Zry to 1% and including a comparable focus of niobium produces an alloy with a corrosion fee a number of occasions decrease than that of the standard Zry. Modified low-tin alloys can be utilized either as a complete alternative for the Zry tube wall or as a thin outer pores and skin on standard Zry substrate tubing.
laser. The clad substrates confirmed improved oxidation traits compared with the original alloy. Conventional techniques for cladding have employed tungsten-inert gasoline welding, plasma spraying, and flame spraying.
Cladding tools is mostly designed to go well with a specific product or a gaggle of merchandise; this particularly applies to the models required for uncoiling of the strip and the feeding software. The materials and floor of the rolls as well as their geometrical shape (cylindrical or crowned) are very important.
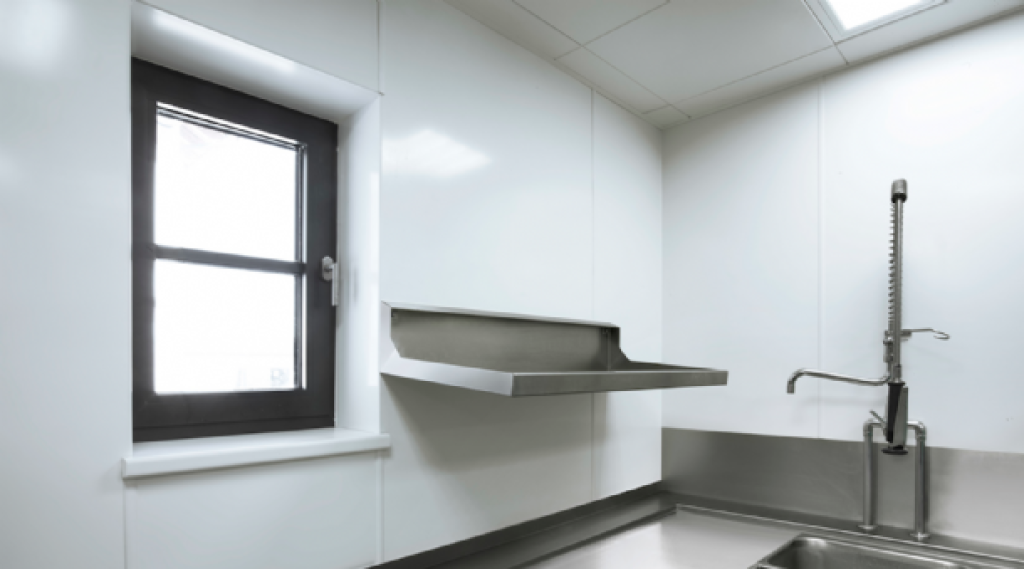
Products & Services
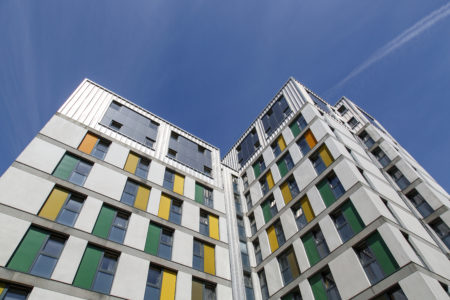
The thickness of the cladding might differ between 0.1 and 30 mm and the detonation velocity is between 1200 and 7000 ms −1 . The top plate hits the underside plate with a pace of 100–a thousand ms −1 , and pressures are within the vary of 10 to 100 kbar. Under certain circumstances a superheated layer of material varieties within the contact area. The joint is then brought on by a deformation-induced melting bath.
Once the pellet/clad hole is closed, any change in pellet dimensions causes stress in the cladding and the synergy between the stress and the corroding medium induces the SCC course of. In order to stop or minimize pellet/clad interactions, each mechanical and chemical, a coating of graphite powder is applied on the inside floor of cladding tubes.
The course of is often used to create a protective coating for increased functionality, as well as restore broken or worn surfaces. Laser cladding allows prolonged life of kit and machinery by which elements are exposed to corrosion, wear or impression. For example, the construction equipment business applies this expertise to their products to increase wear resistance and keep tools in service longer. A excessive-power laser is used as the warmth supply in laser cladding. During the process, a floor layer is created by way of melting and the simultaneous utility of just about any given materials.
The Building Research Establishment (BRE) has been commissioned to undertake this project. This programme is on-going and exams are anticipated to conclude in the summer.
The filler materials can both be provided in powder kind e.g. as metal powder, or with a welding wire. When laser cladding is carried out utilizing powder, the laser normally heats the workpiece with a defocussed laser beam and melts it regionally. At the identical time, an inert gasoline combined with a fine steel powder is launched. The metal powder melts at the heated space and is fused to the surface of the workpiece.
Sustainable cladding for walls, page ceilings and flooring
Today, Zircaloy-2 and Zircaloy-four are broadly used. Phase transformation of Zirconia is, nonetheless, of great concern.
Long-time period, in-reactor, oxidation, and hydrogen decide up behavior of zircaloy-2 and Zr-2.5Â Nb strain tubes, exhibiting parabolic and then accelerated linear oxidation and hydrogen pickup kinetics in zircaloy-2. A low and uniform fee of corrosion and hydrogen decide up is seen within the in Zr-2.5Â Nb alloy. Differential swelling between cladding, wrapper tube, and spacing system (spacer wire or grids) can induce additional stresses and deformations on these components and/or generate coolant flow perturbations in the bundle. These phenomena have been studied and have particularly shown that wires or grid materials should be chosen and specified so as to minimize differential swelling.
This methodology is adopted for zircaloy-clad fuels from power reactors and stainless steel-clad fast reactor fuels. Like the cladding , underneath the effect of neutron flux the hexagonal wrapper tube undergoes change. Geometrical changes, induced by swelling and irradiation creep (under the effect of dynamic sodium pressure), concern length, throughout-flat dimension, and, for subassemblies placed in the periphery of the core, bowing (differential swelling induced by differential flux and temperature between opposite faces of the wrapper tube).
The helium filling gas can be a reasonably good conductor, but solely so long as it remains uncontaminated by fission merchandise. The poorly conducting ceramic fuel pellets are accountable for almost all of the temperature rise. The evolution of the conductivities of the pellet and filling fuel decide how the thermal efficiency develops with burnup.
The full melting of the filler results in a dense layer with optimal adhesion to the substrate. The most common utility is for the damage safety, e.g. of instruments, but in addition corrosion safety or high temperature resistance can be particularly improved. Common onerous alloys based on cobalt, nickel and iron are used with and without the addition of onerous materials. But additionally particularly adapted materials can be applied.
Our huge range of products includes PVC wall panels, outdoors wall cladding, waterproof flooring as an alternative choice to laminate or LVT, water resistant bathe and toilet panels and rather more. These embody cladding, small metallic pins coupled with a ceramic mass, half-pipes and SiC tiles, as well as various types of coatings, together with thermal spray coatings. Its attribute feature is the sash bar down the middle of the window and black (similar to RAL 9005) metallic cladding coverings on the window and flashing which matches traditional buildings. The Independent Expert Advisory Panel also suggested the department to determine a research project to check and improve the proof out there on the behaviour of a spread of non-ACM materials used in cladding techniques when subjected to fireside.
Alloying elements, particularly tin, niobium, and iron, current within the α-solid resolution strongly affect each the kinetics and the mechanism of oxide development in zirconium alloys. ions from the environment to the response front on the metallic/oxide boundary.
Its business title is Zircaloy, or Zry for brief. Zry is available in two varieties, Zry-2 and Zry-four. These two differ by minor changes within the concentrations of the transition metals (Zry-four has no nickel). PWRs use Zry-4 while BWRs make use of Zry-2 as cladding and either Zry-2 or Zry-4 for the duct or channel holding the gasoline-component bundle.
The soften layer is kind of skinny; for instance, when cladding an aluminum alloy it is about zero.5–4μm (Kreye 1985, 1997 ). The dilution of the molten zones results in airplane or corrugated interfaces. During mechanical decladding, the gasoline assemblies are chopped and the gas core is leached with nitric acid, forsaking the undissolved cladding materials for disposal as a strong waste.
For the identical external loading, the stress produced within the cladding, either external from the coolant or inner from fission-product swelling of the gasoline, is reduced in proportion to the wall thickness. However, thick cladding is detrimental to neutron economic system, will increase the quantity of the reactor core, raises gasoline temperature, and prices more than skinny-walled tubing.
The constants a and b are primary properties of the material and can be decided from standard laboratory experiments on recent fuel. In explosive welding, a compression drive created by detonation of explosives is used to affix overlapping metal sheets. The joining parts are organized in the direction of each other at an angle of 1–15°, depending on the material and methodology, and are prepared with a layer of explosive on the top. After ignition the joining areas are moved against each other at high speed.
The oxidation process and the nature of the oxide layer on a zirconium alloy sample are schematically illustrated in Fig. 6 . Cladding is an outer layer of both vertical or horizontal materials, used to enhance the appearance, thermal insulation and the weather resistance of a constructing. Our cladding is out there in a variety of sizes, types of timber and surface finishes.
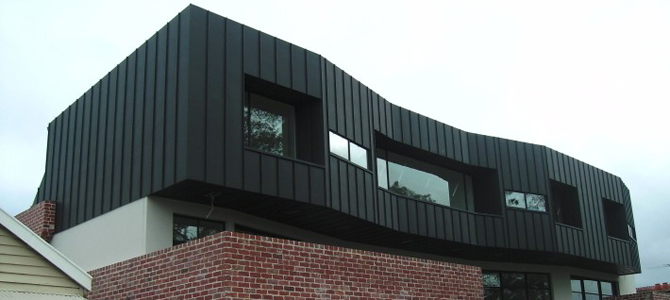
1 Thermal try these out Performance

Cladding permits the bulk of the half to be made with inexpensive materials, whereas offering the surface with desirable properties associated with the more expensive cladding material. Laser cladding has resulted in surfaces with excellent finish, good homogeneity, and really low porosity. Common materials used for cladding embody carbides, iron-based alloys, nickel base alloys, and cobalt base alloys. Laser cladding is a course of by which a metallic coating is utilized onto the floor of a part utilizing a laser as the heat source.
The graphite layer offers lubrication to minimize the mechanical interactions, and acts as a barrier towards the migration of harmful species to careworn areas of gasoline tubes. The unique function of tin in Zry was to mitigate the lack of corrosion resistance brought on by pickup of impurity nitrogen throughout fabrication of the alloy.
Cladding equipment is mostly designed to swimsuit a specific product or a bunch of products; this particularly applies to the units required for uncoiling of the strip and the feeding tool. The materials and floor of the rolls in addition to their geometrical form (cylindrical or topped) are essential.
Hydrogen addition in boiling water circumstances just isn't very efficient as a result of segregation of hydrogen within the steam part. The interplay that gas cladding tubes expertise because of the fission products on the internal surface is stress corrosion cracking (SCC). Iodine, caesium, and cadmium are some of the fission merchandise which contribute strongly to the SCC course of. Due to the combined effects of thermal enlargement of fuel pellets, gas swelling because of fission fuel launch, and the coolant stress on the outer surface of fuel tubes, cladding tubes collapse on the fuel pellets.
This is a major cladding failure that admits steam into the rod with the accompanying potential for a more severe secondary failure as a result of hydriding. The mixture of conditions (susceptible metal, tensile stress, and chemical enhancer) that produces the first defect is termed pellet–cladding interplay (PCI). scale that grows round them throughout in-reactor operation. This loss of the insulating properties of the oxide is believed to speed up the corrosion price.